What Is Vibration Testing?
Vibration testing is a laboratory-based mechanical testing method designed to assess how a product or component responds to vibrational stressors across a defined range of frequencies and amplitudes. These stressors are engineered to mimic real-world conditions that the product may encounter during transportation, installation, or operation. Vibration testing can be applied during various stages of the product lifecycle—from early R&D and prototype validation to final product qualification and regulatory approval. By subjecting test specimens to controlled vibration profiles, engineers can uncover mechanical weaknesses, assess structural integrity, determine potential fatigue points, and simulate conditions leading to functional failure.
This form of environmental testing is especially vital in industries where products must endure ongoing motion, cyclic stress, or mechanical shock. Common applications include the automotive sector (engine mounts, suspension systems), aerospace systems (avionics, flight instrumentation), consumer and industrial electronics (PCBs, batteries), medical devices (infusion pumps, implantable electronics), and protective packaging for goods in transit. Vibration testing ensures not only mechanical durability but also helps validate quality standards and regulatory conformance, ultimately safeguarding brand reputation and minimizing the risk of recalls, warranty claims, or safety failures.
Why Is Vibration Testing Important?
Vibration testing serves several key purposes throughout the product development lifecycle, from early-stage prototyping to post-production quality control. It is used to simulate operational stresses and ensure products meet performance expectations in real-world conditions. By reproducing the types of vibration a product might encounter during use or transit, engineers can identify weaknesses, refine designs, and validate reliability.
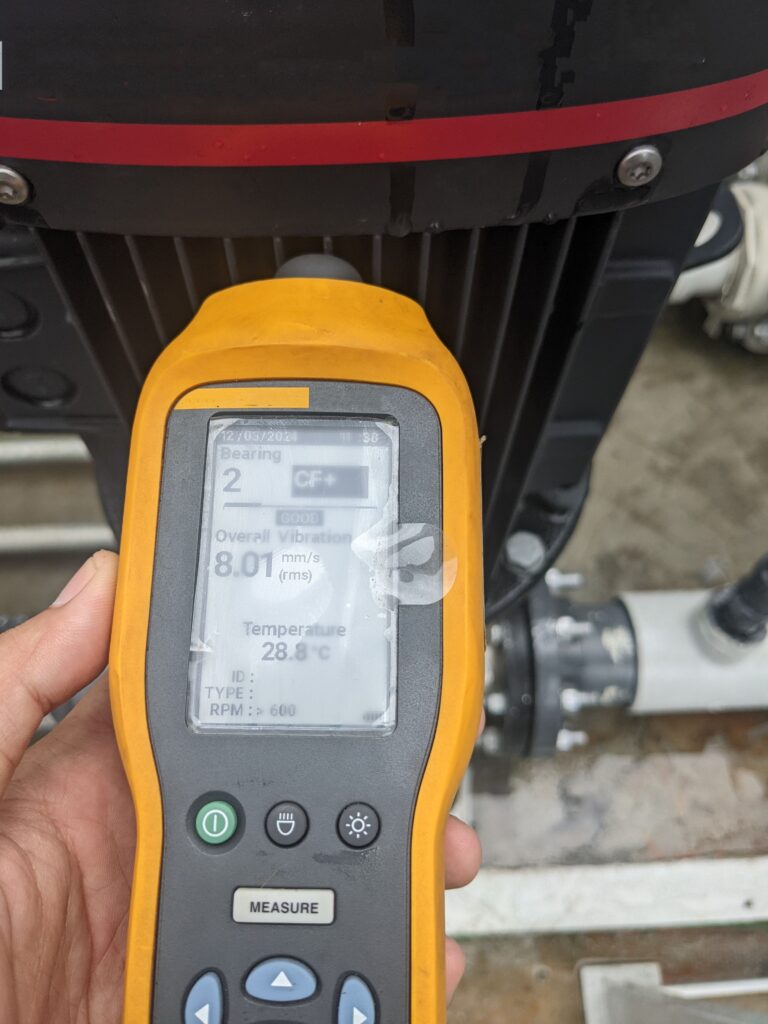
- Product Reliability and Durability: Vibration testing confirms whether a product or component can withstand the dynamic forces encountered during operation or transportation. This is particularly critical for products that will be shipped over long distances, installed in moving vehicles, or used in environments where continuous vibration is expected. Testing helps extend product life and avoid unexpected failures.
- Design Validation: During early development, vibration testing is used to uncover potential design flaws or structural vulnerabilities. It can reveal weak joints, poor material choices, or component misalignments before mass production. Identifying and resolving these issues early saves time and costs while improving product safety and performance.
- Compliance Testing: Many industries require vibration testing to meet specific standards before a product can be certified or sold. These standards—such as MIL-STD-810 for military equipment, ISTA protocols for packaging, and ISO 10816 for rotating machinery—define the vibration profiles and thresholds products must pass. Adhering to these guidelines ensures regulatory approval and market acceptance.
- Failure Analysis: If a product fails in the field or during transit, vibration testing can help simulate those conditions to determine the root cause. By recreating real-world vibrations in a controlled lab environment, engineers can pinpoint the mode and mechanism of failure—such as metal fatigue, component loosening, or cracking—and implement corrective actions.
Without vibration testing, manufacturers risk launching products that may fail due to unseen vulnerabilities, particularly in high-stakes applications like aerospace systems or medical implants.
How Are Vibration Tests Performed?
Vibration testing typically involves placing a sample on a vibration platform or shaker table that reproduces specific frequencies, amplitudes, and waveforms. The three main test categories are:
1. Sinusoidal Vibration Testing
Sinusoidal vibration testing involves applying a pure sine wave to a test item, either at a fixed frequency or across a swept frequency range. This type of testing is designed to identify the resonance frequencies of components or assemblies, where vibrations may be amplified and potentially lead to failure. It is commonly used to validate structural performance, assess fatigue behavior, and evaluate the mechanical robustness of items subjected to consistent vibrational patterns. Industries such as aerospace, defense, and consumer electronics frequently rely on sinusoidal testing to simulate operational conditions in engines, turbines, or onboard electronics.
2. Random Vibration Testing
Random vibration testing simulates more realistic, complex vibration environments by applying multiple frequencies simultaneously over a given frequency bandwidth. This type of testing mirrors the unpredictable and multidirectional forces experienced during transport or field operation, such as those encountered in shipping, driving, or launch conditions. It is widely used in the validation of packaging systems, automotive assemblies, satellite components, and other products that must endure varying vibration loads during transit or use.
3. Mechanical Shock Testing
Mechanical shock testing evaluates a product’s ability to withstand sudden, extreme force inputs that can occur during drops, impacts, or explosions. These high-intensity pulses can range from simple free-fall drops to programmed shock pulses that simulate collision or blast effects. Shock testing is critical for military-grade hardware, aerospace systems, and shipping containers that may experience accidental or hostile impact forces. The results help manufacturers improve packaging design, component mounting, and overall product durability.
In some cases, vibration testing is combined with climatic chambers to expose products to thermal cycling, humidity, or other stressors during testing (known as HALT—Highly Accelerated Life Testing).
Products and Components That Require Testing
A wide range of products and assemblies undergo vibration testing as part of regulatory or quality requirements. These tests help determine how components perform under real-world conditions such as transportation, mechanical operation, and prolonged environmental exposure. The goal is to ensure that products maintain their structural integrity, functionality, and safety over their intended lifespan, especially in high-risk or mobile applications. Vibration testing is an integral part of quality assurance, often mandated by standards or used during product development to assess performance and durability before release.
Common examples include:
Product Category | Vibration Testing Purpose |
---|---|
Automotive components | Assess fatigue of mounts, dashboards, and powertrains |
Aerospace systems | Verify durability of avionics, satellites, landing gear |
Electronics | Evaluate solder joint integrity and PCB resilience |
Medical devices | Ensure implantable or transportable devices stay secure |
Consumer goods | Test packaging strength and resistance to transit damage |
Industrial machinery | Identify resonance and premature wear in mechanical parts |
Shipping containers | Simulate handling and transport-induced vibration exposure |
Vibration testing may be performed during prototype development, pre-shipment inspections, or as part of lifecycle qualification testing.
Vibration Testing Standards
Industry-specific standards ensure consistency, accuracy, and comparability in vibration testing procedures across various sectors. These standards define test parameters such as frequency ranges, amplitude levels, duration, axis orientation, and acceptance criteria, making them essential for product qualification, certification, and regulatory compliance. By adhering to established standards, manufacturers can demonstrate that their products meet the durability expectations of end-users, logistics providers, and government regulators. These standards also help testing laboratories maintain best practices, minimize variability, and support repeatable test results.
Key examples include:
- MIL-STD-810G/H – U.S. military standard for environmental engineering testing
- ISTA Series (e.g., ISTA 1A, 3E) – International Safe Transit Association packaging vibration protocols
- ASTM D999 – Standard test methods for vibration of shipping containers
- ISO 10816 – Guidelines for mechanical vibration severity in rotating machinery
Compliance with these standards is often mandatory for regulated products, especially in aerospace, defense, and medical sectors.
Partnering with Testing Laboratories
Third-party testing laboratories provide expert testing services using advanced equipment and adherence to regulatory guidelines. By outsourcing this specialized testing, companies benefit from:
- Access to calibrated electrodynamic and hydraulic shaker systems
- Environmental chambers for combined testing (temperature, humidity, vibration)
- Detailed test reports for certification or submission to regulatory bodies
- Cost-effective validation during prototyping, production, or shipment
ContractLaboratory.com connects companies with ISO/IEC 17025-accredited laboratories experienced in performing:
- Transportation simulation and shipping vibration testing
- Aerospace and defense compliance testing
- Custom vibration fixture design and data acquisition
Submit Your Vibration Testing Request Now
Final Thoughts
Vibration testing is a critical step in ensuring product performance, safety, and compliance in dynamic environments. From vehicle components to consumer packaging, vibration exposure can impact product functionality and customer satisfaction.
By incorporating rigorous vibration testing into their development and quality workflows—and by partnering with experienced testing laboratories—manufacturers can bring more resilient and reliable products to market.